RECYCLED PLASTIC MATS…..HOW DO THEY DO IT?
THE RECYCLING PROCESS
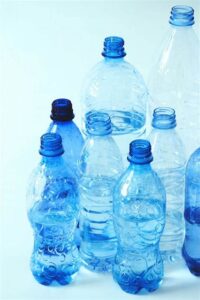
Water bottles ready to be recycled
Everyday people all over the world consume liquids from polypropylene bottles. These bottles are what soft drinks, milk and water are commonly found in and in the past have found their way into landfill. These products do not breakdown over time and why the movement to create more and more products using recycled materials is becoming important to consumers.
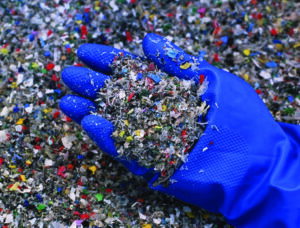
Shredded Water Bottles
Once bottles are collected from us through local recycling programs etc, the plastic bottles are taken to a recycling plant where they are put through a shredder cutting the bottles into small pieces. Lids of bottles cannot be recycled easily therefore they are excluded by machine from the recycling process. The plastic pieces are then washed to remove any labels and sticky residue.
See how your bottles are shredded to make our raw materials.
Recycled plastic is then heated and melted to create small pellets that are then sold to manufacturing companies that use polyester and polypropylene in the manufacturing of their products just like they do for our mats created for Camping Mat Warehouse.
WE USE ONLY UV STABILISED MATERIALS
Exposure to UV light, whether from sunlight or indoor lighting, can lead to the degradation of most plastics. This degradation process can begin during manufacturing or once the product is in use, resulting in symptoms like brittleness, discolouration, and a loss of key physical properties such as impact and tensile strength, as well as colour fading. This deterioration ultimately shortens the lifespan of the plastic.
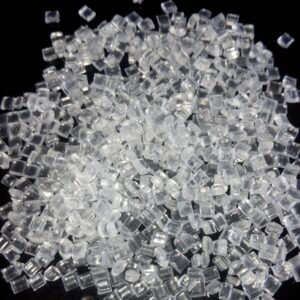
UV Stabilised pellets
For instance, a common scenario of UV degradation is seen in outdoor furniture like plastic lawn chairs, which often become discoloured and brittle over time due to exposure to sunlight.
To counteract this issue, as manufacturers of outdoor matting we incorporate UV stabilisation additives. These additives are chemical compounds added in very small amounts to our raw product. They effectively help stop the deterioration caused by UV light, significantly extending the durability and lifespan of our mats.
HOW THE PLASTIC AND UV MATERIALS BECOME A MAT
The raw recycled plastic pellets along with a percentage of new plastic and UV stabilised pellets are all combined and mixed. Our ratios used is propriety as there are other manufactures of recycled mats who have not quite got it right and their mats do not last in Australian conditions like ours.
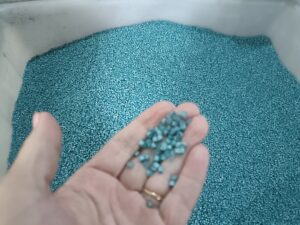
Coloured pellets
Our colour specialist mixes dyes and adds to a large hopper that contains the pellets. It spins and mixes they dye coating plastic to the required colour. This is when our first quality audit is completed to ensure colour matches as per colour chart.
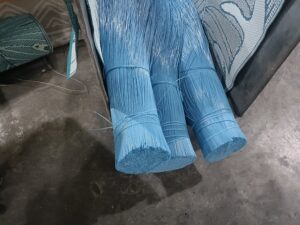
One piece straws used for mat weave
The colour pellets are then placed in a large hopper linked to a melting machine. The pellets are heated and extruded into straws per our required thickness. The thickness we use ensures that our mats are soft underfoot but also the most durable mats on the market. The straws are then cut into the required length to ensure they are one continuous strand. Our machines can handle up to 3m wide mats therefore our mats will never be “glued” together or have a seam sewn into it.
The straws and then transferred to one of our our weaving machines. UV stabilised threads and our coloured straws and then woven using computer software to create a mat with our required design size and specifications. All edges are heat pressed to ensure strength and durability in our final product.
The mats come out on a large roll and are cut using heat technology again to the required size. At this stage our mats go through their second quality control audit to ensure mats are being woven to the correct specifications.
BINDING AND EYELETS
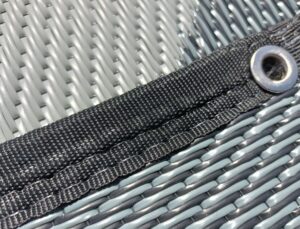
Double Stitching in polyester thread with stainless eyelets
All binding, including the stitching, is crafted from UV-stabilised polyester materials. The binding not only enhances the aesthetic finish of our mats but also provides a robust foundation for our stainless steel eyelets. We use one of the widest bindings available to ensure maximum strength and durability for our mats. Unlike cotton, polyester threads are chosen specifically for their UV-resistant properties, contributing to the longevity of our products.
Our stainless steel eyelets are installed using a specialized machine designed to accommodate the thickness of our mats and binding. These eyelets are invaluable for securing the mat firmly to the ground, especially during windy conditions.
PACKAGING AND BAGS
After our mats undergo final inspection, where meticulous hand-folding ensures top-notch quality, correct sizing, and adherence to our specifications, they are carefully packed into PVC-lined carry bags. These bags offer numerous advantages: they prevent moisture from spreading to other items in your vehicle when the mat is packed while allowing fresh air to circulate around it, reducing potential odours caused by dampness. Keeping the bag open on one side is key; closing it could lead to unwanted smells and make cleaning more challenging upon arrival home. Our bags are crafted for durability and strength, designed to endure.
Made from polypropylene, our mats are lightweight—each meter weighs approximately 1kg—and boast stain and mildew resistance. They are woven for breathability, ensuring they protect rather than harm the grass underneath, even withstanding spills like red wine.
Our deep understanding of these products stems from years of experience with various mat brands. This expertise enables us to guarantee the high quality necessary for our mats to thrive in the harshest conditions they encounter.
Want to know the difference between our mats and others? Check this info out. Why choose our mats!